Vous avez fêté il y a trente ans le millionième, et plus récemment le deux millionième tracteur construit à Mannheim. Quelles ont été les évolutions notables aux cours de ces trois décennies ?
Le premier changement manifeste qui me vient à l’esprit, c’est la complexité accrue des tracteurs. A l’époque, quand vous vous teniez à une extrémité de la chaîne de montage, vous pouviez voir la fin de l’autre côté. Aujourd’hui, il y a des caisses tout le long, et toutes sortes d’outils et d’appareils qui pendent du plafond. Ça n’a plus rien à voir, ce sont deux mondes différents. Il y a trente ans, il n’y avait presque pas d’électronique sur les tracteurs. Il y avait une pompe d’injection mécanique, et en cas de panne, il suffisait en général de réparer le câble d’accélérateur pour que tout reparte.
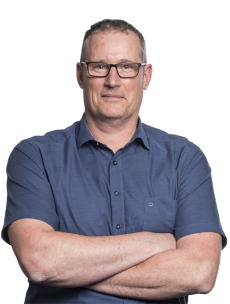
Dans les années 2000, les tracteurs ont été complètement électrifiés. L’injection électronique a remplacé l’injection mécanique. Tout d’un coup, la pédale d’accélération est devenue un petit potentiomètre à monter. Puis est apparu le pont avant suspendu. Là où auparavant il y avait deux ou trois unités de contrôle, il y en a aujourd’hui six, voire huit. À cela se sont ajoutés tous les éléments de commande électroniques, avec aujourd’hui 14 voire 16 unités dans le plus grand modèle. En raison de la grande complexité technique et de la quantité des variantes, de nombreuses étapes de travail ne peuvent plus être effectuées directement sur la chaîne de montage et doivent être externalisées.
Avez-vous un exemple concret pour illustrer cette évolution, dans le cadre de votre travail quotidien ?
Le prémontage des capots moteur est un bon exemple. Ça a été l’une de mes premières tâches en tant que jeune mécanicien industriel, en 1992. À l’époque, ces capots étaient entièrement en tôle, donc sans pièces en plastique. Je montais en tout une trentaine de pièces : la charnière, deux vis, la calandre à phares, le joint en caoutchouc, quelques tringles… et c’était fini ! Il faut comparer cela avec les capots de nos tracteurs forte puissance d’aujourd’hui, qui comportent à eux seuls 250 vis…
La quantité des variantes a aussi augmenté. Auparavant, on pouvait choisir entre deux options de configuration pour la signalisation lumineuse, l’une pour la circulation à droite, l’autre pour la circulation à gauche. Aujourd’hui, il y a les feux de croisement et de route, LED ou non LED, et tout ça à la fois pour la circulation de droite et celle de gauche. Beaucoup de choses ont évolué. Le contenu du travail lui-même a été de plus en plus optimisé et condensé.
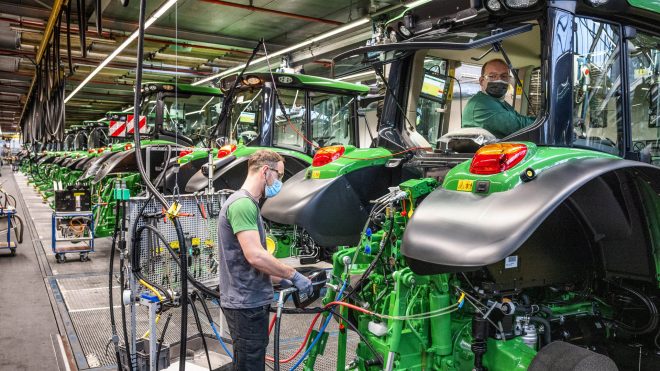
Comment parvenez-vous à maîtriser cette complexité à l’usine ?
C’est un travail qui s’est fait pas-à-pas. Une force de notre usine est que beaucoup des employés y travaillent depuis très longtemps. Le personnel a donc évolué en même temps que l’usine, et peut mettre son expérience au service de chaque défi à relever. Les équipes ont appris la complexité avec le temps, sans même vraiment s’en rendre compte. De plus, la production est aujourd’hui très assistée par l’automatisation, et les équipes sont plus nombreuses qu’auparavant. C’est nécessaire pour continuer à assurer nos missions avec rapidité et fiabilité.
Quel rôle joue l’automatisation ?
Aujourd’hui, à Mannheim, de nombreux domaines sont extrêmement automatisées. Par exemple celui de la production des pièces, où ce sont des robots qui contrôlent les fraiseuses ou les tours. L’assemblage final est aussi concerné : autrefois, on assemblait le châssis à la main dans un gabarit. Aujourd’hui, c’est le robot de la station de vissage qui s’en charge.
En tant qu’employés, nous bénéficions donc d’un appui croissant, ce qui évidemment profite aussi à l’ergonomie. Un point important à ce sujet : l’automatisation doit viser à alléger le travail des équipes, et donc être à leur service. Ils sont porteurs de tout un savoir-faire – et c’est avec eux que je veux continuer travailler à l’avenir.
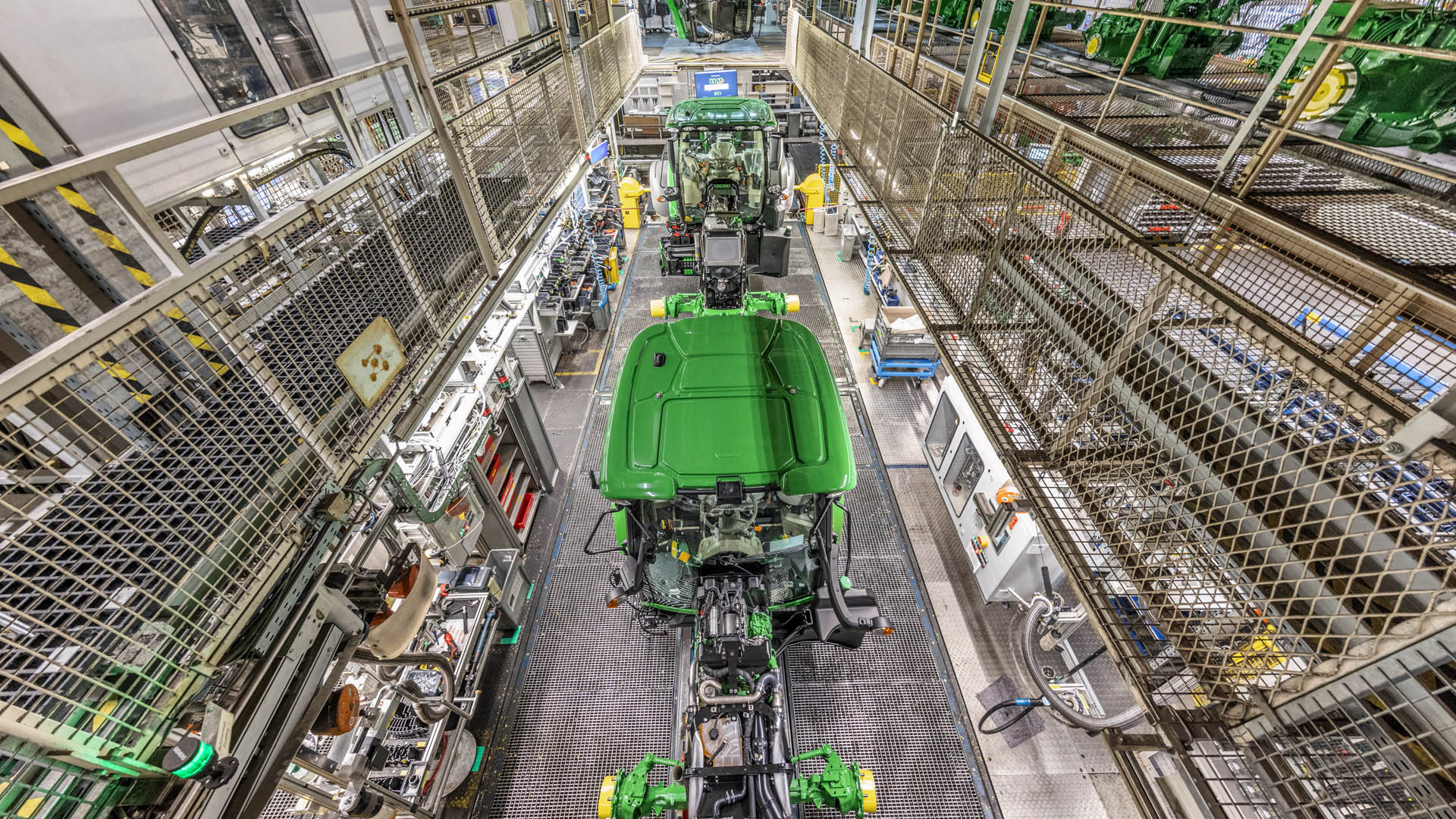
Pour vous personnellement, quels ont été les moments forts des dernières décennies ?
J’ai trouvé formidable l’idée d’ouvrir l’usine aux visiteurs. Ce concept n’existait pas du tout avant. Nous ouvrir davantage vers l’extérieur a été un beau pas en avant. J’ai grandi dans le voisinage immédiat de l’usine, mais jusqu’à peu de temps avant le début de ma formation, j’ignorais tout de ce qui se passait de l’autre côté de ses murs de brique rouge. Aujourd’hui, les gens des alentours connaissent nettement mieux l’entreprise et font tout de suite le lien quand je leur explique que je travaille chez John Deere.
Un autre moment fort a certainement été la façon dont nous avons réussi à surmonter les problèmes de disponibilité des pneus. Nous ne pouvions pas nous permettre d’abandonner la construction des tracteurs le temps que la livraison soit de nouveau assurée de manière fiable. Nous nous sommes dit : « Pourquoi ne pas construire des tracteurs sans pneus ? » Nous en avons donc construit 800, qui n’en ont été équipés qu’après-coup. Cela nous a permis de continuer la production malgré les problèmes de livraison. Notre devise est la suivante : « impossible » n’existe pas.

Comment résumeriez-vous vos 35 ans passés chez John Deere ?
Globalement, je dirais que John Deere m’a donné l’opportunité de passer du statut d’apprenti à celui de cadre, tout en voyant l’usine se développer. C’est très valorisant.