L’usine John Deere de Mannheim est en pleine effervescence. Les tracteurs se déplacent sur convoyeur qui traverse l’ensemble de l’atelier de production, d’un poste d’assemblage à l’autre. D’étape en étape, le châssis initial se transforme en tracteur avec cabine, capot, pneus et phares. Depuis quelques mois, les machines, à mi-parcours de la chaîne, doivent également passer sous une grande structure en forme d’arche. Des lumières bleues au sol marquent le début ce cette nouvelle étape, une des dernières évolutions en matière d’assurance qualité : le système SkyHawk.
Ce nom de superhéros désigne un robot mobile sur 7 degrés de liberté et équipé de caméras de pointe. Le système contrôle minutieusement les tracteurs avant l’installation de la cabine, du capot et d’autres composants sur les postes suivants.
Un œil attentif
La caméra SkyHawk examine 50 points de contrôle en 3 minutes et compare l’état du tracteur avec une banque d’images référençant les caractéristiques recherchées.
Détecter les écarts de production
Produire des tracteurs de la plus haute qualité possible : c’est l’objectif numéro un pour tous les employés de l’usine. « Le projet SkyHawk intègre dans notre propre production le concept de base de la technologie See and Spray mise au point pour nos clients », commente Linus Baumhauer, directeur du site. « Tandis que, pour les exploitants, il s’agit d’une application ciblée des produits phytosanitaires, nous utilisons SkyHawk pour détecter et éviter les écarts de production à un stade précoce. »
Nous utilisons SkyHawk pour détecter et éviter les écarts de production à un stade précoce.
Linus Baumhauer
L’idée est d’utiliser un robot qui reproduise des séquences de mouvements humains, mais soit aussi à même de reconnaître et d’interpréter les résultats de l’assemblage au moyen du traitement d’images industrielles. « Cela nous permet de maîtriser la charge de travail du personnel tout en contrôlant la qualité de nos produits de manière entièrement automatisée. »

Tobias Trunk, responsable de l’automatisation de l’usine de Mannheim, est responsable de la conception et du design du système SkyHawk. Avec son équipe, il a d’abord dû trouver une solution pour intégrer harmonieusement le système d’inspection dans la structure de l’usine, qui s’était développée au fil des ans.
« À l’échelle mondiale, il n’existe qu’une poignée systèmes similaires, et tous sont installés en parallèle de la chaîne de montage, ce qui réduit la complexité car le robot peut alors déplacer la caméra plus facilement vers toutes les parties du véhicule. Mais ce type d’installation n’était pas une praticable pour nous, dans la mesure où l’espace dont nous disposons ne pouvait accueillir qu’un système de portillon qui enjambe la ligne de fabrication, au-dessus des tracteurs. »
Pour que la caméra puisse inspecter chaque recoin du tracteur, elle est montée sur un robot à six axes qui se déplace également d’avant en arrière sur un rail linéaire, au-dessus de la machine.
Afin de calibrer le fonctionnement du système, Tobias Trunk et son équipe ont d’abord développé un prototype entièrement numérique, qui leur a permis de tester le concept de manière approfondie. La deuxième étape a consisté à installer le dispositif dans un atelier vide de l’usine de Mannheim. « Nous avons dû surmonter quelques obstacles, notamment pour que le matériel et le logiciel fonctionnent en parfaite harmonie. Nous devons être en mesure de cartographier et de tester un large éventail de variantes », indique Tobias.
Des délais serrés
Les mouvements de la caméra autour de chaque modèle de tracteur sont soigneusement programmés par les experts, de même que les points d’inspection, où la caméra doit s’arrêter brièvement. Tout se base sur les modèles numériques des tracteurs : la caméra ne survole pas le tracteur physique qui se trouve devant elle, mais un « habit » numérique qui recouvre la machine. SkyHawk reçoit des informations sur le modèle à tester et sa configuration par le biais d’une puce RFID placée dans le bouchon du réservoir de carburant.
Après de longues heures consacrées au codage et à une multitude de tests, l’équipe a finalisé SkyHawk pour une utilisation en conditions réelle. L’installation du système sur la chaîne de production s’est déroulée sur une période fixe de 14 jours correspondant aux congés du site de Mannheim. Durannt ces deux semaines, l’équipe a démonté le système SkyHawk dans l’atelier d’essai pour le réinstaller dans l’atelier de production de tracteurs. « Ça a été une période très intense pour chacun d’entre nous », se souvient Tobias Trunk. « Mais comme nous avons tous travaillé en équipe, le système a été opérationnel à temps au moment où la production a repris. »
L’installation de SkyHawk
Le système a été monté durant les 14 jours de fermeture de l’usine de Mannheim.
Coopération homme-machine
Dès les premières heures et pendant plusieurs jours après le déploiement de SkyHawk, Tobias Trunk et son équipe sont restés présents en permanence pour remédier rapidement aux difficultés de démarrage et éliminer les bugs éventuels. Le système est maintenant en service depuis plusieurs mois. Il a fait ses preuves et la ‘coopération’ avec ses collègues humains est désormais parfaitement fluide. Dans chaque zone de production, un des employés porte à cet effet une montre connectée au poignet qui reçoit une alerte lorsque SkyHawk détecte une anomalie. La montre indique directement l’écart mesuré par rapport aux valeurs prescrites. Il peut ainsi se rendre directement au poste SkyHawk et régler le problème avant que celui-ci n’entraîne une réaction en chaîne.
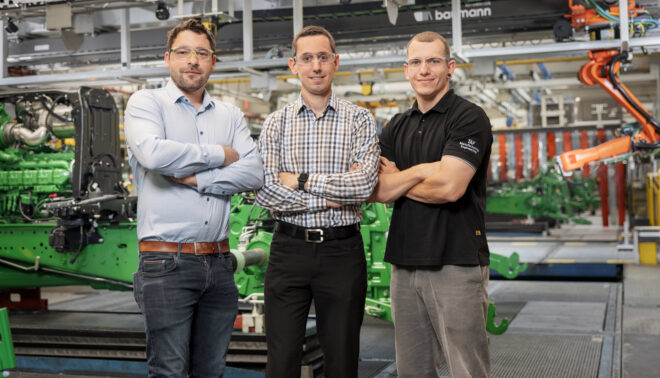
« Le projet SkyHawk montre que nous pouvons intégrer dans notre chaîne de production des technologies qui continue à améliorer la qualité de nos tracteurs, tout en simplifiant la tâche de nos employés », se félicite Tobias Trunk. « C’est tout l’intérêt de l’automatisation. »