Comment le personnel de l’EPDC contribue-t-il à la satisfaction des clients John Deere ?
À vrai dire, c’est assez simple. Nous savons que la disponibilité des pièces, associée à l’expertise du service concessionnaires, est la clé de la satisfaction du client. C’est particulièrement vrai pendant les récoltes, où le facteur temps jouent un rôle crucial, notamment lorsque des précipitations sont attendues. Notre équipe a bien conscience que les clients – agriculteurs ou ETA – ne peuvent pas travailler correctement sans un approvisionnement rapide et fiable en pièces détachées. C’est pourquoi nous travaillons 363 jours par an pour garantir la livraison aussi réactive que possible de toutes les pièces au catalogue.
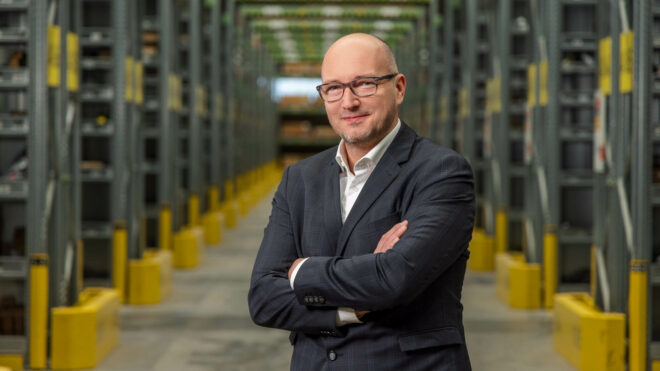
Comment garantissez-vous cette disponibilité ?
Comme je l’ai évoqué plus haut, ce sont en particulier les commandes de dépannage, notamment durant les chantiers de récolte, qui jouent un rôle important. Nous sommes en capacité de préparer les pièces pour l’expédition en 45 minutes. C’est notamment possible grâce à un flux de données sophistiqué, qui fait la jonction entre les systèmes automatisés de stockage et de transport, et les étapes de travail manuelles. Il s’agit d’harmoniser l’interface humain-technologie.
Toutes les commandes ne nécessitent pas une livraison immédiate. Cela ne nous empêche pas d’améliorer en permanence nos processus internes, de la réception des pièces au stockage et à la livraison. L’analyse des données nous aide à déterminer l’emplacement de stockage optimal pour chaque pièce. Par ailleurs, l’interaction l’homme-technologie est sans cesse affinée, pour rendre la circulation des pièces détachées dans l’entrepôt plus fluide.
Nous pouvons empaqueter et affranchir nous-mêmes des pièces à expédier par avion dans une région distincte. Le client gagne ainsi un temps précieux à la livraison. Enfin, que les propriétaires d’engins agricoles plus anciens se rassurent : nous stockons les pièces pendant au moins 15 ans après l’arrêt de la production d’une série.

L’EPDC entrepose près de 350 000 références. Comment cela se traduit en termes de gestions des stocks ?
Là aussi, nous nous appuyons sur l’analyse des données, notamment celles générées par les machines connectées. La connaissance du parc global de matériels, doublée d’évaluations statistiques, permet une prévision de plus en plus fine de la demande. Nous nous assurons ainsi d’avoir les pièces nécessaires en stock – à l’EPDC, mais aussi dans les concessions. Cette approche de planification proactive est un argument de vente unique dans le secteur : dans l’idéal, une pièce est toujours disponible auprès de la concession et peut y être récupérée directement par le client.
Quels sont les défis actuels du secteur logistique et comment y répondez-vous ?
C’est avant tout la pénurie d’employés qualifiés. Nous nous efforçons de rendre l’environnement de travail plus attractif, par exemple en perfectionnant l’ergonomie et en proposant des postes à temps partiel. De cette manière, nous espérons notamment inciter davantage de femmes à travailler au sein de l’EPDC. Nous essayons aussi de faire face à la hausse des coûts logistiques, qu’il s’agisse des péages, du carburant, ou du prix des emballages. Grâce à une planification judicieuse, nous sommes à même de grouper 96 % des commandes de nos concessionnaires, de façon à ne procéder, par exemple, qu’à une seule livraison au lieu de trois. Nous évitons ainsi des coûts et des émissions CO₂, ce qui va dans le sens du développement durable.
Concernant la durabilité, que fait l’EPDC pour réduire son impact carbone ?
Nous sommes l’un des premiers sites John Deere à avoir installé, ici à Bruchsal, un système photovoltaïque sur le toit de nos bâtiments, en service depuis maintenant 10 ans. Il couvre 12 % de notre consommation d’énergie. À quoi s’ajoutent, générées à partir d’autres sources d’énergie renouvelable sur site, 18 % de nos besoins en électricité, et toute la chaleur nécessaire au chauffage et d’autres processus du site.
Nous réduisons aussi la quantité de plastique dans le matériau de remplissage pour nos expéditions, et nous le remplaçons par du papier de rembourrage spécialement traité. Nous avons aussi introduit des emballages contenant 30 % d’herbe pour les petites livraisons. La production de ces emballages mobilise moins d’eau et d’énergie, ce qui réduit de manière significative leur empreinte carbone.
Outre les activités directement réalisées sur le site, une bonne planification a aussi un impact positif sur la chaîne d’approvisionnement. Le nombre de livraisons à court terme à pu être revu à la baisse grâce à de meilleurs pronostics. Cela signifie moins de fret aérien et donc, là encore, moins d’émissions.
L’EPDC en chiffres
99,7 %
c’est la fiabilité de livraison de l’EPDC. Ce chiffre n’est jamais descendu en dessous de 99 %, même au plus fort de la pandémie.
En cas de besoin, nous pouvons préparer des commandes de dépannage en
45 minutes
seulement.
Près de
350.000
références sont stockées au sein de l’EPDC.
Vous dirigez l’EPDC depuis l’automne 2023. Quelles ont été vos premières impressions ?
J’étais déjà en contact avec l’EPDC lors de mon précédent poste de directeur du service clientèle. Certaines des problématiques du centre m’étaient déjà familières, et je connaissais sa réputation de performance.
C’est avant tout la complexité des processus qui m’a impressionné – le haut degré d’automatisation mis en œuvre, et la manière dont d’innombrables rouages fonctionnent en parfaite harmonie. J’ai aussi été immédiatement frappé par la bonne ambiance qui règne aux sein des équipes, avec plus de 650 employés au total. La satisfaction des clients est au cœur de leur travail quotidien, avec beaucoup de respect dans les interactions entre collègues, et un niveau élevé de professionnalisme et d’expérience dans l’exécution des tâches. Dans ce contexte, il n’est pas étonnant que le Comité d’entreprise parle toujours de l’« esprit de Bruchsal. » Cela décrit très bien l’ambiance familiale du site.